What is Synthetic Fiber?
Fibers and fabrics play a large role in everyday applications. A fiber is a hair-like strand of material. They are the smallest visible unit of a fabric and are denoted by being extremely long in relation to their width (at least 100 times longer than it is wide). Fibers can be spun into yarn and made into fabrics.
Synthetic fibers are a subset of the larger area of textiles. Textiles can be natural or synthetic. Natural fibers include cotton, fur, wool, etc. Regenerated fibers are natural materials that have been processed into a fiber structure. Regenerated fibers such as cellulose and wood pulp are used to make materials such as rayon and acetate. Synthetic fibers are man made from chemicals. They are generally based on polymers and are stronger than natural and regenerated fibers.
How Synthetic Fibers and Fabrics are Made:
Most synthetic fibers go through a similar production process which includes four steps.
Chemical Pocess:
A chemical process usually polymerization, prepares and combines the components for the fiber. Polymerization is the formation of macromolecules through repetition of basic units. Initially, the various components are solids and first must be converted to a liquid state to be extruded into fibers. The materials are chemically converted, dissolved, or melted, turning into a thick liquid.
Spinning Process:
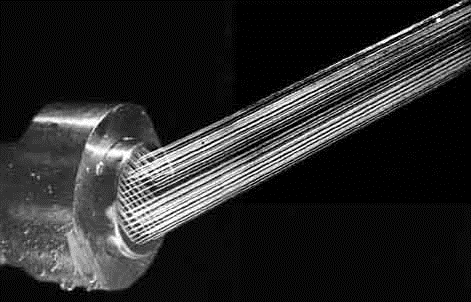
A spinning process produces the fiber by passing the thick liquid through a spinneret. A spinneret is a device with hundreds of holes of a specified diameter. The liquid is forced through the spinneret holes and comes out a string liquid filament. The hole in the spinneret determines the diameter of the filament, which is set by the application. The extrusion is dried to a continuous filament fiber.
Twisting Process:
A twisting process twists the filament fiber into a yarn. The filament falls vertically from the spinneret and is caught in a large vacuum nozzle. The vacuum force keeps tension on the line as it is wound around a bobbin.
4. The twisted yarn is packaged and sent to a textile mill.
Material Specifications for Synthetic Fibers:
In order to determine the polymer to use, key properties of polymer should be identified. These properties include:
- Composition and structure- The type of polymer, the amount/length of side chains, and the shape of the polymer. The shape and amount/length of side chains plays an important role in the strength of the polymer.
- Melting point– The temperature at which the polymer begins to melt. Melt strength is a property which indicates the polymer’s ability to withstand drawing without breaking. This is improved with the presence of high molecular weight tail or long chain branches.
- Modulus– The ability of a material to resist deformation. The property is usually expressed as the ratio of stress exerted on the sample to the amount of deformation.
- Elasticity and recovery from strain– The elastic limit is the stress at which the uniaxial stress-strain curve becomes nonlinear due to shear yielding or crazing. Shear yielding is the irreversible slipping of molecule chairs and crazing is the formation of low density, crack-like volumes which scatter light (this makes the polymer look white).
- Tensile- These properties are the most important indication of strength and stiffness of the material. They determine the force necessary to pull the specimen apart, and the deformation before breaking. The tensile modulus is a measure of stiffness calculated based on measured force.
- Density– The weight per unit volume. Density affects physical properties like stiffness, impact strength, and optical properties.
- Moisture absorption- The amount of moisture a fiber will absorb from the air at a standard condition of 70°F and a relative humidity of 65%.
- Dye-ability- The ability of the polymer to absorb and hold on to a dye.
- Comfort– How the material feels to the user. If the fiber or fabric is going to be used in apparel then the comfort stretch (freedom of movement when wearing the fabric), phase change ability, and hydrophobic nature should be considered.
Applications of Synthetic Fibers:
Synthetic fibers and synthetic fabrics are used in a variety of industries and applications, including:
- Aerospace
- Apparel or clothing
- Architecture and construction
- Automotive and transportation
- Chemical processing
- Electrical
- Electronics
- Filtration
- Marine
- Medical
- Safety
- Welding
Specialized products can also be used to control electrostatic discharge (ESD) and provide shielding from electromagnetic interference (EMI) and radio frequency interference (RFI).